As with all things in life it's good to have options. I have worked out which 25mm ID wheel bearings will work in a five spoke front wheel from a K12 series bike (see another post on the forum, dunno exactly where at the mo')....but desired to also have a workable axle solution for the stock dimension 20mm ID bearings. Here is the preliminary design in brief.

Here the roughcut axle protrudes from the fork leg. This end will be lopped off approximately 20mm from the outside edge of the fork leg and a 10mm hole drilled through for easy axle removal with a 'Tommy bar'. The metal is 4140 and has been tested for strength at a metals specialty firm which electrically tests for hardness and
stretchability. Since it's not stainless steel the exposed end of the new axle will be etched and primed, and the areas of the axle inside or under collars will be slathered with anti-sieze compound to minimise corrosion.

This end eventually gets tapped for the 10x20mm screw that 'pulls' all of our early K bike's axles and seating collars snug, and in concert with the four fork leg bolts,
pinch the axle. Note the 25mm OD sleeve which takes up the slack around the 20mm diametre of the new axle. How do we intend to secure this end of the axle if it doesn't tighten sufficiently? We don't want the end screw and the opposite ends pinch bolts to have to do all of the work. We'll slice this 25mm collar from end to end so that it becomes a shim and is able to be tightened against the axle by the two fork end pinch bolts - but only if it requires it. We'll know this when the axle is fully machined and the threads tapped. The stock, internal 20mm axle centre spacer between the original bearings is utilised. New bearings are going in when the axle is fully ready.
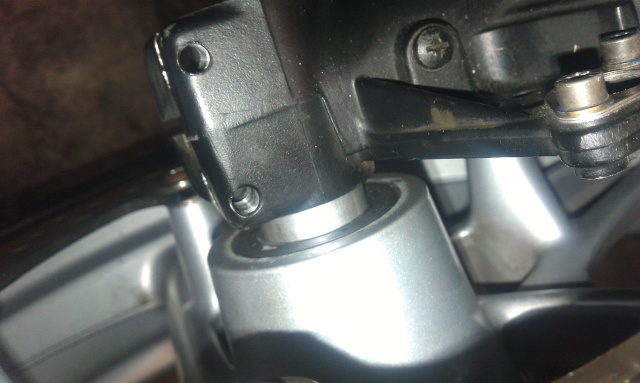
Here the OEM axle spacer has been shortened about 40% from stock so it just slips inside the wheel seal and seats against the inner bearing race.

Here the stock axle collar seats neatly up against the entire outside edge of the sealed wheel bearing. No adjustments need to be made to this side collar since it's the wide end of the axle where the fork lower 'floats' or self-centres.

Here the heads of the rounded Torx

screws which hold down the 305mm brake discs to the wheel (from an F Series GS, same discs as an R12 Series GS) have been machined down about 1.5mm so they clear the inside edge of the Marzocchi fork legs as the wheel spins. Clearancing the fork legs a few mm's right where the screw heads pass by is an option as well. You decide which is tidier.
The ABS sensor bracket will be ground away cleanly, the forks refinished and the incongruous ABS warning sticker will be removed as this bike is gunna be
sans ABS.
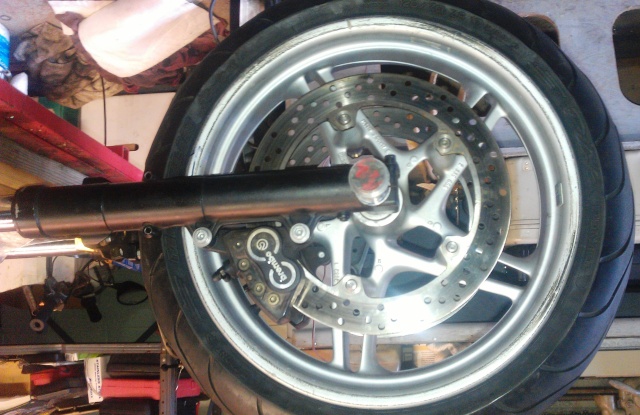
The entire fork assembly, brakes and wheel are clamped down to a work table to facilitate access - a few big words for making things a whole lot f*ck*ng easier. The wheel and discs centre into the middle of the callipers. Any
minute adjustments to centre things up as needed can be made by adding or removing those wavy shims behind the brake disc mounting points.
The bloke who's fabricating this axle for me is a machinist for a Tacoma firm that makes hatches for nuclear subs and valves for nuclear power plants. This is kinderplay and he's enjoying it - will save the plans for making additional axles as needed by anyone else. He rides a coupla different Beemers, a new R1200GS
Wasserboxer, R1200ST, as well as a Guzzi and several Harleys. The bloke who has volunteered his workshop space is currently a K75S rider but has had a few Airheads and a K100RS. They're happy to see this idea through. I will owe them both a bottle of something warm and peaty, preferrably single malt.