1
Build reinforced replacement for broken Fairing Rear tabs Tue Apr 23, 2013 5:15 am
ibjman

Life time member
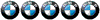
Tonight while prepping my rs fairing lowers for some paint re-coating, I decided to dive in with both feet and try to repair the long standing broken rear tabs. It seems that every set of older lowers I ever see has the rear tabs broken off at the speed nut.
NOTE: Let me apologize to all for the obviously sloppy workmanship and lack of proper detailing of the parts in the photos after the repair. I am not happy with the appearance of the insides of the parts that don't show after installation. That said, I feel the repair is solid and warrants sharing with others as these seem to be difficult to get fixed in a way that lasts. I'm sorry it turned out so "Rough" looking, but I have little patience and/or skills for hours of fine sanding & grinding with micro tools to smooth out all the unseen surfaces.
To start out, I realized that there's a critical little "ledge" molded in to the bottom edge of the upper fairing rail near the broken rear tab, (Photo #3). This ledge appears to be for maintaining the side to side edge alignment of the lower against the upper when installed.



I was fortunate to have a damaged upper fairing available to use for a "mold" to help accurately form the new surfaces on the broken lower. I elected to mold the entire ledge surface from the upper in to the rail of the lower although this differs from the original design. I felt that the original design was "marginal" at best when it comes to strength of the flange rail that supports the fastening tabs. By choosing this option I was more free to add bulk and thickness to the new section I was adding to the lower to support the tab screws. I felt that having all 3 sides of the protruding ledge from the upper flange duplicated into the lower might increase it's rigidity, hence overall durability.
In order to start the repair, I added a strip of cellophane packing tape to the original flange rail on the upper, so that I could release the lower away from it after the materials set up.

Next (with the main fairing upside down in the bench) I installed the broken lower with all the screws, including a new speed nut on the broken tab position. Next, a strip of aluminum tape was added along the edge of the for a surface to form the fiberglass fill material against. Turns out I didn't do it very well, but I hope it will give you all the idea. (pictures #5 & #6 directly below should be in reverse order).
NOTE: The surface where the new repair material is to be added must be thoroughly ROUGH sanded or ground for the new material to stick. WEAR A RESPIRATOR. TINY FIBERGLASS SHARDS WILL DAMAGE YOUR LUNGS.
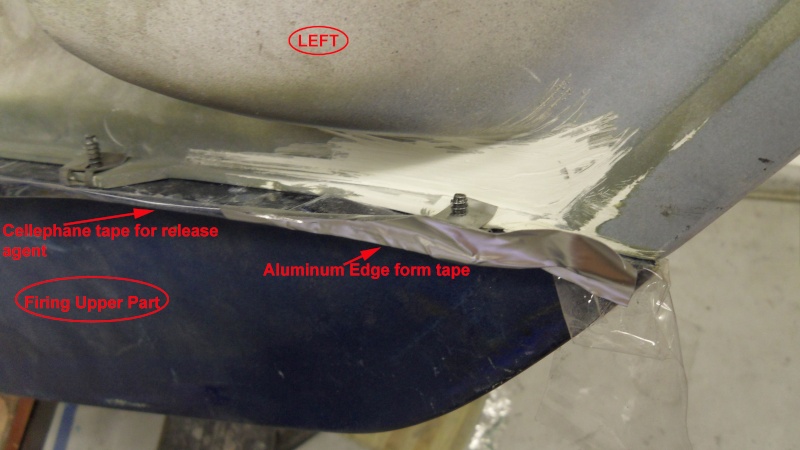

Now I mixed up the repair material, a stranded pre saturated fiberglass material often known in the industry as "Kitty Hair". Scooping out a small dollop and adding the required epoxy hardener material. Stir this stuff very well to insure a good even mix, but work quickly as it sets up in about 10 minutes.
You must wok in a well ventilated area. This material seems to have very toxic fumes. I wear a respirator as a good practice, as it is essential for sanding, grinding & shaping operations of the fiberglass after it's set. It's best to just get in the habit of wearing this to protect your lungs.

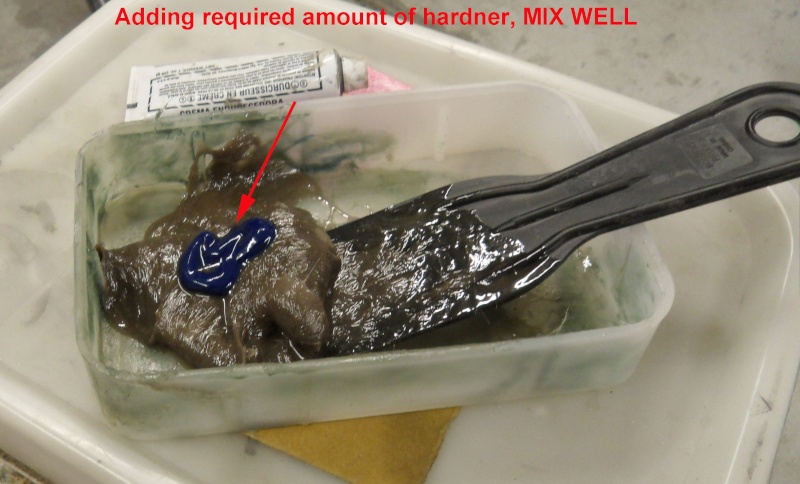
Once mixed, lay the mixture in to the area where the new flange/tabs are desired. It must be against rough clean "Fibron" fiberglass casting material to have the proper adherence. As long as I had a batch of the sticky stuff mixed up, I prepped and repaired both lowers in one step.
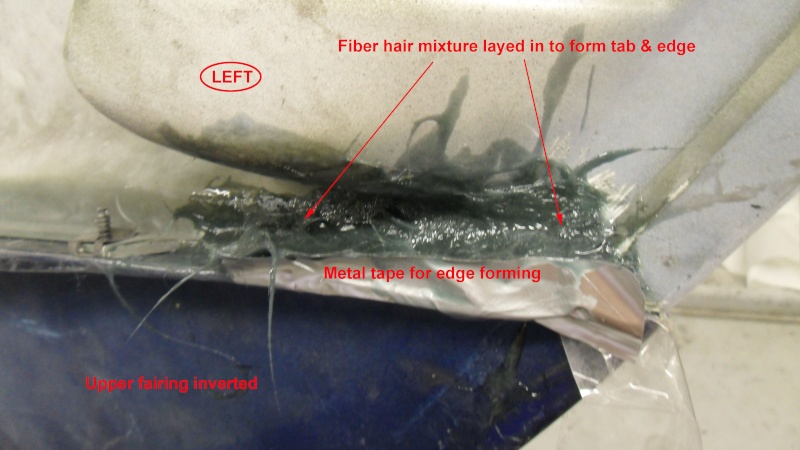

After about 15 - 20 minutes the repair material will be nicely set. You'll notice it gets quite warm from the epoxy chemical reaction. As soon as it's quite firm to the touch, remove the screws and peel the lower section carefully away from the upper. Because of the cellophane tape layer, it won't be stuck on permanently. In my project, I elected to permanently mold the rear most speed nut into the new material. I felt this allowed me more flexibility in forming up a broad extra strong flange area and also do the job more quickly.
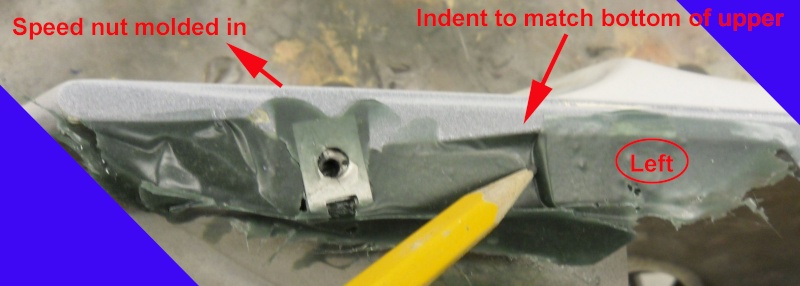

After the parts are molded in, It may be necessary to temporarily test fit the lowers to your actual upper to determine which places need to be trimmed and sanded to allow the proper clearance for all the fairing parts to mesh together & fit well. I had to drill a new hole for the screw just forward of the one we were fixing that holds the forward edge of the knee pad/fairing filler dress piece "wedge", as well as a small relief out of the top edge of the new flange material to allow clearance for the edge of the speed nut that secures it. You'll see the ugly gouged out area there around the second hole from the end. I'm sorry that this isn't more nicely finished & smoothed, but my time was limited for this repair.
Also, I had to remove a fair bit of material from the rear corner (overhang) of the new flange material in order that the knee pad/filler could lay fully down flush against the rear slanted edges of the assembly.


I hope this will make someone else's journey through this fix a little easier. It was meant to be at least informative, if not beautiful.
The appearance in the photos is so poor that I was embarrassed to claim it.
Regards, ibj...
NOTE: Let me apologize to all for the obviously sloppy workmanship and lack of proper detailing of the parts in the photos after the repair. I am not happy with the appearance of the insides of the parts that don't show after installation. That said, I feel the repair is solid and warrants sharing with others as these seem to be difficult to get fixed in a way that lasts. I'm sorry it turned out so "Rough" looking, but I have little patience and/or skills for hours of fine sanding & grinding with micro tools to smooth out all the unseen surfaces.
To start out, I realized that there's a critical little "ledge" molded in to the bottom edge of the upper fairing rail near the broken rear tab, (Photo #3). This ledge appears to be for maintaining the side to side edge alignment of the lower against the upper when installed.



I was fortunate to have a damaged upper fairing available to use for a "mold" to help accurately form the new surfaces on the broken lower. I elected to mold the entire ledge surface from the upper in to the rail of the lower although this differs from the original design. I felt that the original design was "marginal" at best when it comes to strength of the flange rail that supports the fastening tabs. By choosing this option I was more free to add bulk and thickness to the new section I was adding to the lower to support the tab screws. I felt that having all 3 sides of the protruding ledge from the upper flange duplicated into the lower might increase it's rigidity, hence overall durability.
In order to start the repair, I added a strip of cellophane packing tape to the original flange rail on the upper, so that I could release the lower away from it after the materials set up.

Next (with the main fairing upside down in the bench) I installed the broken lower with all the screws, including a new speed nut on the broken tab position. Next, a strip of aluminum tape was added along the edge of the for a surface to form the fiberglass fill material against. Turns out I didn't do it very well, but I hope it will give you all the idea. (pictures #5 & #6 directly below should be in reverse order).
NOTE: The surface where the new repair material is to be added must be thoroughly ROUGH sanded or ground for the new material to stick. WEAR A RESPIRATOR. TINY FIBERGLASS SHARDS WILL DAMAGE YOUR LUNGS.
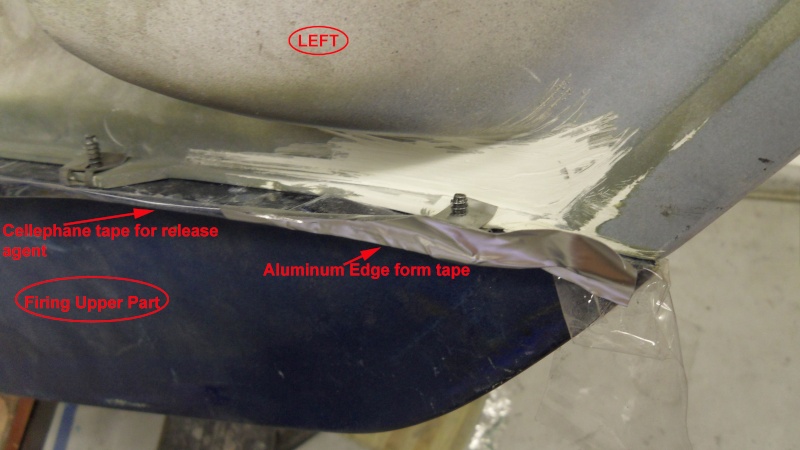

Now I mixed up the repair material, a stranded pre saturated fiberglass material often known in the industry as "Kitty Hair". Scooping out a small dollop and adding the required epoxy hardener material. Stir this stuff very well to insure a good even mix, but work quickly as it sets up in about 10 minutes.
You must wok in a well ventilated area. This material seems to have very toxic fumes. I wear a respirator as a good practice, as it is essential for sanding, grinding & shaping operations of the fiberglass after it's set. It's best to just get in the habit of wearing this to protect your lungs.

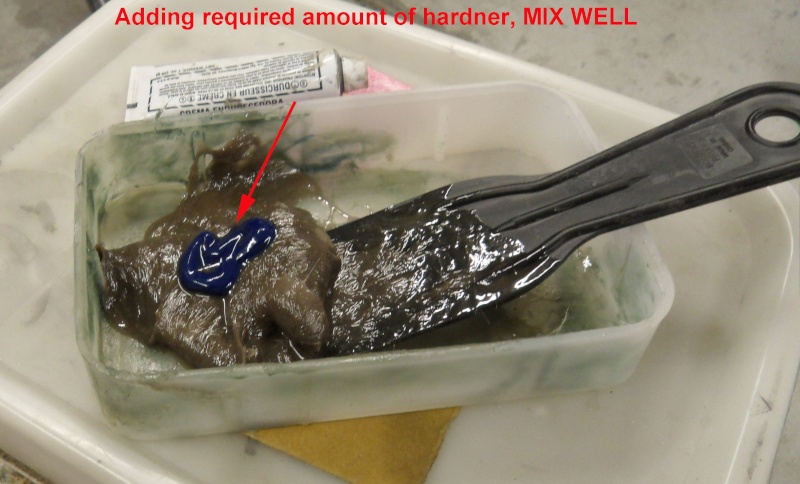
Once mixed, lay the mixture in to the area where the new flange/tabs are desired. It must be against rough clean "Fibron" fiberglass casting material to have the proper adherence. As long as I had a batch of the sticky stuff mixed up, I prepped and repaired both lowers in one step.
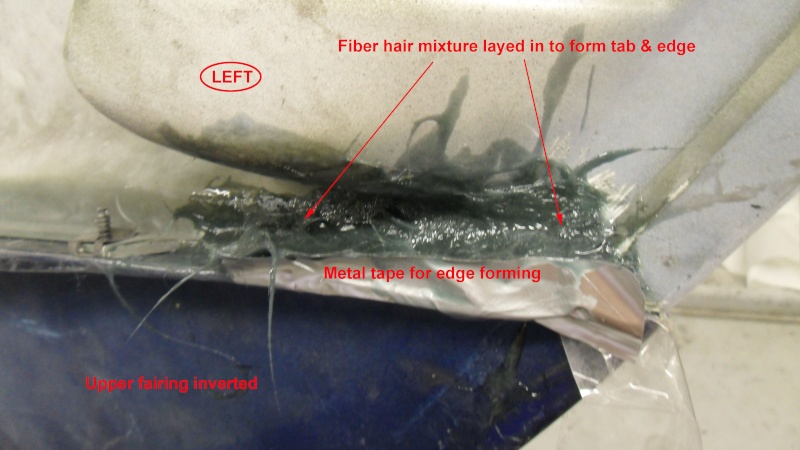

After about 15 - 20 minutes the repair material will be nicely set. You'll notice it gets quite warm from the epoxy chemical reaction. As soon as it's quite firm to the touch, remove the screws and peel the lower section carefully away from the upper. Because of the cellophane tape layer, it won't be stuck on permanently. In my project, I elected to permanently mold the rear most speed nut into the new material. I felt this allowed me more flexibility in forming up a broad extra strong flange area and also do the job more quickly.
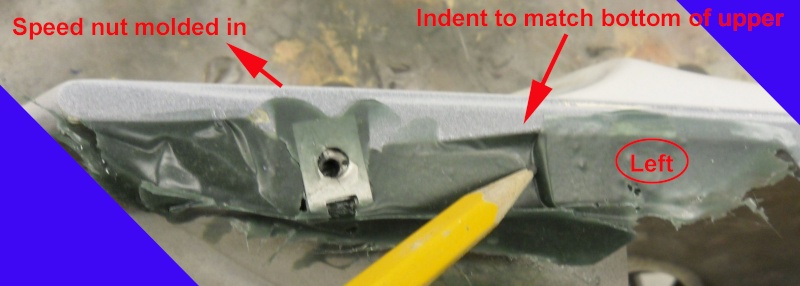

After the parts are molded in, It may be necessary to temporarily test fit the lowers to your actual upper to determine which places need to be trimmed and sanded to allow the proper clearance for all the fairing parts to mesh together & fit well. I had to drill a new hole for the screw just forward of the one we were fixing that holds the forward edge of the knee pad/fairing filler dress piece "wedge", as well as a small relief out of the top edge of the new flange material to allow clearance for the edge of the speed nut that secures it. You'll see the ugly gouged out area there around the second hole from the end. I'm sorry that this isn't more nicely finished & smoothed, but my time was limited for this repair.
Also, I had to remove a fair bit of material from the rear corner (overhang) of the new flange material in order that the knee pad/filler could lay fully down flush against the rear slanted edges of the assembly.


I hope this will make someone else's journey through this fix a little easier. It was meant to be at least informative, if not beautiful.
The appearance in the photos is so poor that I was embarrassed to claim it.
Regards, ibj...