1
Digital readouts for your lathe. Wed Apr 18, 2012 5:41 pm
sidecar paul

Life time member
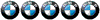
Here's something for all the lathe owners out there.
When cheap digital calipers became easily obtainable, they are now selling at less than £10 in the UK, I thought it would be a good way of fitting DRO's to my lathe. All the ones I have bought have been remarkably accurate when checked with my gauge blocks, so no problem there.
The first job is to remove the jaws either by sawing, if the material is soft, or grinding.
The cross slide fitting is straightforward, with 6" of movement being adequate for most lathes, and a couple of brackets are all that is needed. If the material is too hard to drill then a small clamp may be required.
Be careful not to damage the 'plastic' strip on the arm, as the caliper works by measuring the capacitance of this strip as it moves.

The saddle readout is more of a problem as the saddle moves more than the 6 or 7 inches that you can squeeze out of a caliper, my saddle moves about 24",so I solved this by making a sliding block. When measurement is not required, the readout moves with the saddle.
When measuring, the clamp lever locks the readout to the bed and movement of the saddle pulls the arm through the readout.


This system has served me well for quite a few years already and I can't remember when I last needed to turn something longer than 6"........ it was probably fork spindles for a 1924 Longstroke Sunbeam that I used to have.
The big advantages are no backlash in the slide movements, instant switch between imperial and metric and instant zeroing of readouts.
I haven't put too much detail here as there are many different lathes, but if you can use a lathe then you should be able to adapt the idea.
Cheers,
Paul.
When cheap digital calipers became easily obtainable, they are now selling at less than £10 in the UK, I thought it would be a good way of fitting DRO's to my lathe. All the ones I have bought have been remarkably accurate when checked with my gauge blocks, so no problem there.
The first job is to remove the jaws either by sawing, if the material is soft, or grinding.
The cross slide fitting is straightforward, with 6" of movement being adequate for most lathes, and a couple of brackets are all that is needed. If the material is too hard to drill then a small clamp may be required.
Be careful not to damage the 'plastic' strip on the arm, as the caliper works by measuring the capacitance of this strip as it moves.

The saddle readout is more of a problem as the saddle moves more than the 6 or 7 inches that you can squeeze out of a caliper, my saddle moves about 24",so I solved this by making a sliding block. When measurement is not required, the readout moves with the saddle.
When measuring, the clamp lever locks the readout to the bed and movement of the saddle pulls the arm through the readout.


This system has served me well for quite a few years already and I can't remember when I last needed to turn something longer than 6"........ it was probably fork spindles for a 1924 Longstroke Sunbeam that I used to have.
The big advantages are no backlash in the slide movements, instant switch between imperial and metric and instant zeroing of readouts.
I haven't put too much detail here as there are many different lathes, but if you can use a lathe then you should be able to adapt the idea.
Cheers,
Paul.
__________________________________________________
'84 K100RS (0014643) (owned since '85), 86 K100RS (0018891) with Martello sidecar (built as an outfit in '88),
'51 Vincent (since '67),'72 Montesa Cota (from new), '87 Honda RS125R NF4 (bought 2015)
....No CARS never ever!